一种石墨烯的制备方法与流程
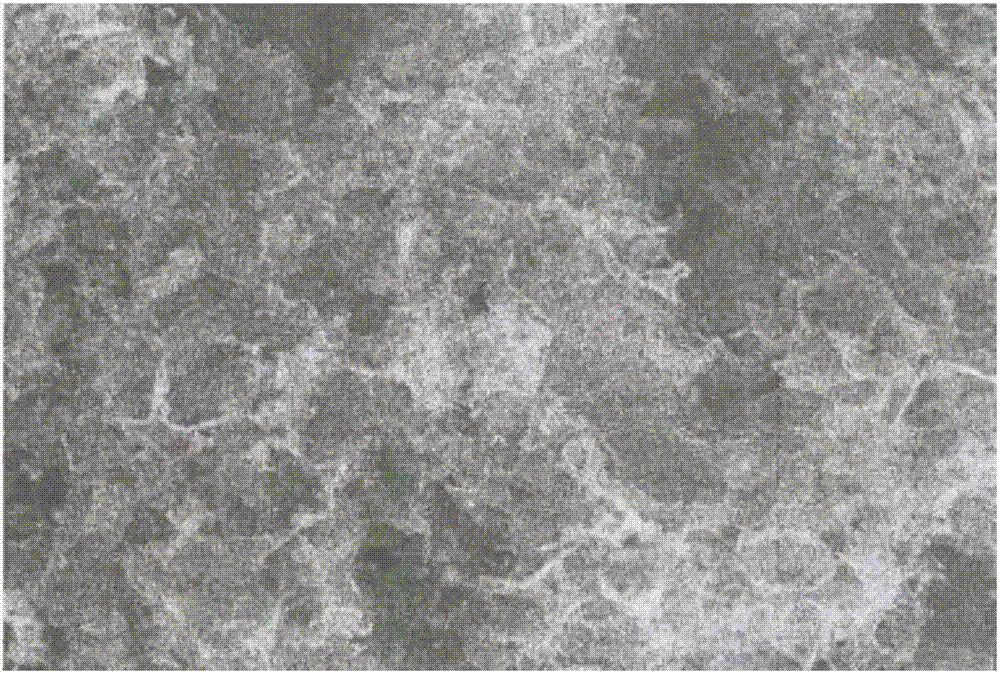
本发明属于材料制备技术领域,特别是涉及一种石墨烯的制备方法。
背景技术:
石墨烯(graphene)是一种由碳原子以sp2杂化轨道组成六角型呈蜂巢晶格的平面薄膜,是一种只有一个碳原子厚度的二维材料,又叫做单原子层石墨,是目前世上最薄的纳米材料。
石墨烯几乎完全透明,吸光率只有2.3%,透光性能非常好,且导热系数高达5300w/m2·k,高于碳纳米管和金刚石。石墨烯的特殊结构性能对新材料及军事科技都有很大的用途,可用于隐形飞机、军舰、坦克、雷达等设备的外体,用作遮光隔热、导热、散热、耐高温等材料。石墨烯在常温下的电子迁移率超过15000cm2/v·s,比纳米碳管和硅晶体高,可用于制造性能更好、更轻、体积更小的输导线及晶体管,而且石墨烯的电阻率仅约为10-6ω·cm,比铜、银更低,是目前电阻率最小的材料,因此为微纳电子器件、电信号大规模输出载体的小型化和轻量化提供了物质支撑。石墨烯可广泛应用于生物医疗领域,如药物传送、癌症治疗和生物传感等。
目前,石墨烯的制备方法有机械剥离法、液体剥离法、化学气相沉积法、氧化还原法等。其中,机械剥离法可获得高品质石墨烯样品,但制作过程非常复杂耗时,产量有限。气相沉积法制备所得石墨烯的面积可任意调整,但其生产工艺复杂、生产环境苛刻,生产成本居高不下,且存在后续转移和分离难度大、成品率低的问题,在真正的商业化应用中仍然有很大的阻碍。氧化还原法能大规模生产石墨烯,但所得石墨烯的氧化基团多,在晶格结构上存在缺陷,性能往往大打折扣。传统液相剥离法是用有机溶剂将石墨进行剥离的,利用有机溶剂插入石墨片层之间,破坏石墨层与层之间的范德华力,同时结合超声波振荡、离心或高速剪切等外部能量输入,获得石墨烯。液相剥离法虽然操作简易、产率高,但需要使用大量的有机溶剂,如n-甲基吡咯烷酮(nmp)、n,n-二甲基甲酰胺(dmf)、二氯苯等,制备方法不环保,对环境危害大,成本高。
技术实现要素:
基于此,本发明的目的在于,提供一种石墨烯的制备方法,其具有操作简单、容易实现、对环境友好且成本较低的优点。
本发明采用的技术方案如下:
一种石墨烯的制备方法,包括以下步骤:
(1)原矿处理:将石墨矿石水洗、晾干后,破碎为矿粉,再浮选矿粉得到精矿粉,然后对精矿粉进行高温除杂、磨细,得到石墨粉;
(2)液相剥离:将步骤(1)所得石墨粉投入弱碱水溶液中浸泡,然后搅拌混合液,再将混合液射流;
(3)后处理:将步骤(2)处理所得的混合液沉淀、过滤,将所得滤渣返回步骤(2)中浸泡,对所得滤液进行泡沫浮选,然后捞取液面的泡沫干燥得到石墨烯,剩余滤液返回步骤(2)中用于浸泡。
其中,步骤(2)采用弱碱水溶液浸泡石墨粉,水分子能插入石墨的片层之间,使层间尺寸扩大,层间的范德华力减弱,水溶液中的氢氧根离子能使石墨片层表面带上相同电荷而相互排斥,进一步减弱层间的作用力,有利于后续石墨烯的剥离;搅拌是对混合液进行高速剪切,并使石墨粉保持分散,射流是指混合液从喷管口、孔口或狭缝等射出,脱离固体边界的约束而扩散流动的过程,射流时混合液中石墨的层与层之间产生剧烈摩擦,通过搅拌和射流的外力作用,吸水后的膨胀石墨的层间实现完全剥离,有效剥离出石墨烯产品。步骤(3)的泡沫浮选是细粒和极细物料分选的方法,是气、固、液三相的相互作用的过程,其中液相作为分选介质,通入的空气或氧气形成气泡携带石墨烯固相上浮,将石墨烯分选出来。
本发明采用液相剥离的方法制备石墨烯,相比于机械剥离和化学气相沉积,其操作更加简单、生产条件要求低、产量更高、成本更低,相比于氧化还原法,其制得的石墨烯不会有其他元素的掺杂、晶格破坏小、品质更高。
一般来说,当溶剂的表面能与石墨烯的表面能接近时,溶剂与石墨烯之间的相互作用可平衡剥离石墨烯所需的能量,适合剥离石墨烯的溶剂的表面张力范围在40~50mj/m2,所以通常使用n,n-二甲基甲酰胺(40.1mj/m2)、n,n-二甲基甲酰胺(37.1mj/m2)等有机溶剂较为合适,然而,尽管这些有机溶剂对于剥离分散石墨烯是有利的,但是其分子大,空间位阻大,插入石墨片层空间缓慢,对石墨烯剥离效率的提高有限。而虽然水的表面能(70mj/m2)明显高于剥离石墨所需的表面能,但是本发明通过在水中加入碱,能在石墨片层表面引入电荷,增大了片层之间的库仑斥力,改善了石墨烯与水溶液的相容性,而且水分子很小,能有效插入石墨片层空间,再结合搅拌和射流的反复外力作用,有利于石墨烯剥离。
因此,相比于传统使用有机溶剂的液相剥离法,本发明的方法同样能有效剥离出石墨烯产品。其次,本发明使用价格更低的弱碱水溶液替代有机溶剂,可使制备成本更低、更安全、对环境污染更小。再者,本发明采用搅拌与射流结合的外力输入方式,比传统液相剥离所用的超声波振荡等方式所需的设备成本也更低。另外,本发明通过优化设计工艺流程,对未剥离出石墨烯的滤渣重复处理,并重复使用提取石墨烯后的滤液,实现了物料循环,减少物料损耗,能有效提高石墨烯产率,每吨混合液可制备得到300~500g石墨烯产品。
进一步地,步骤(1)中,所述石墨矿石的石墨含量为50~80%,所述破碎是利用球磨机将石墨矿石磨碎为200~300目的矿粉,所述磨细是利用雷蒙机将高温除杂后的物料研磨为2000目或以上的石墨粉。球磨机将石墨矿石初步磨碎,便于进行对矿粉浮选和高温除杂,而雷蒙机研磨精度更高,能将高温除杂后的物料进一步磨细,且通过限定雷蒙机研磨颗粒的大小,一方面可避免矿粉颗粒太大不利于液相剥离,另一方面可避免矿粉颗粒过小而导致后续步骤(3)泡沫浮选时泡沫难以单独带起石墨烯,泡沫中的成分复杂,达不到分选效果。
进一步地,步骤(1)中,所述浮选是将矿粉送入浮选机中浮选至含碳量为80~90%的精矿粉。
进一步地,步骤(1)中,所述高温除杂是将精矿粉送入温度为2800~3000℃的高温炉内气化除杂,得到含碳量大于或等于99%的石墨粉。通过将高温炉温度设定在合适的范围,能将精矿粉中的铜、钨、铁等杂矿除去,同时避免温度过高导致石墨软化、熔化。
进一步地,步骤(2)液相剥离为:将步骤(1)所得石墨粉投入装有弱碱水溶液的碱液池中浸泡,再将碱液池内的混合液送入搅拌桶中搅拌,然后将搅拌桶内的混合液通过射流管射流返回到碱液池。弱碱性水溶液比起弱酸性水溶液对石墨的插层效果更好,碱液池、搅拌桶、射流管是常用的化工设备,结构简单、造价低。
进一步地,步骤(2)中,所述弱碱水溶液为碳酸氢钠水溶液,其ph值为7.2~8.3,不会破坏石墨烯的结构,碳酸氢钠俗称小苏打,常用于食品加工,不会对环境造成影响。
进一步地,步骤(2)中,碱液池内混合液中石墨粉的质量百分比不超过0.5%,避免石墨粉浓度过高影响液相剥离效果。
进一步地,步骤(2)中,所述浸泡的时间为2~3h,所述搅拌和射流的时间共1~2h。
进一步地,步骤(3)后处理为:将步骤(2)处理所得的混合液送入沉淀池中沉淀1~2h,然后用2000目或以上的滤网过滤,将所得滤渣返回到步骤(2)的碱液池,将所得滤液送入浮选机中进行泡沫浮选,然后捞取液面的泡沫以70~80℃干燥得到石墨烯,干燥温度过低,生产效率低,而干燥温度过高会使石墨烯被水蒸气带走,造成损耗,剩余滤液返回到步骤(2)的碱液池,完成物料循环。
进一步地,步骤(3)中,所述泡沫浮选时往每吨滤液中投加1~2g浮选药剂,所述浮选药剂为酚黑药、醇黑药或氧烷醇黑药中的任意一种或多种的混合。黑药作为浮选药剂的选择性高、稳定性好,对石墨烯的捕收能力强。
为了更好地理解和实施,下面结合附图详细说明本发明。
附图说明
图1为本发明中石墨烯的制备方法的工艺流程图;
图2为本发明制备方法所得石墨烯样品的显微图像。
具体实施方式
实施例1
如图1所示,本实施例的石墨烯的制备方法按如下步骤进行:
(1)原矿处理:
将产自黑龙江的石墨含量为68%的石墨矿石水洗、晾干后,利用球磨机磨碎为200~300目的矿粉,再浮选矿粉至含碳量为80~90%的精矿粉,然后将精矿粉送入温度为3000℃的高温炉内气化除杂,再利用雷蒙机对高温除杂后的物料进行研磨,得到含碳量大于99%、2000目的石墨粉。
(2)液相剥离:
将步骤(1)所得石墨粉投入装有ph值为8的碳酸氢钠水溶液的碱液池中浸泡2h,并控制混合液中投加的石墨粉的质量百分比不超过0.5%,再将碱液池内的混合液送入搅拌桶中搅拌,然后将搅拌桶内的混合液通过射流管射流返回到碱液池,对混合液循环搅拌和射流操作共2h。
(3)后处理:
将步骤(2)处理所得的混合液送入沉淀池中沉淀2h,然后用2000目的滤网过滤,将所得滤渣返回到步骤(2)的碱液池,将所得滤液送入浮选机中进行泡沫浮选,并选用酚黑药作为浮选药剂,浮选时往每吨滤液中投加2g酚黑药。浮选后,捞取液面的泡沫,用铜片制成的输送带将泡沫送入干燥室内以75℃的温度进行干燥,得到石墨烯,然后对石墨烯包装、入库,浮选后剩余滤液则返回到步骤(2)的碱液池。
实施例2
如图1所示,本实施例的石墨烯的制备方法按如下步骤进行:
(1)原矿处理:
将产自黑龙江的石墨含量为75%的石墨矿石水洗、晾干后,利用球磨机磨碎为200~300目的矿粉,再浮选矿粉至含碳量为80~90%的精矿粉,然后将精矿粉送入温度为2800℃的高温炉内气化除杂,再利用雷蒙机对高温除杂后的物料进行研磨,得到含碳量大于99%、2500目的石墨粉。
(2)液相剥离:
将步骤(1)所得石墨粉投入装有ph值为8.2的碳酸氢钠水溶液的碱液池中浸泡1.5h,并控制混合液中投加的石墨粉的质量百分比不超过0.5%,再将碱液池内的混合液送入搅拌桶中搅拌,然后将搅拌桶内的混合液通过射流管射流返回到碱液池,对混合液循环搅拌和射流操作共2h。
(3)后处理:
将步骤(2)处理所得的混合液送入沉淀池中沉淀1h,然后用2500目的滤网过滤,将所得滤渣返回到步骤(2)的碱液池,将所得滤液送入浮选机中进行泡沫浮选,并选用酚黑药作为浮选药剂,浮选时往每吨滤液中投加1.5g醇黑药。浮选后,捞取液面的泡沫,用铜片制成的输送带将泡沫送入干燥室内以80℃的温度进行干燥,得到石墨烯,然后对石墨烯包装、入库,浮选后剩余滤液则返回到步骤(2)的碱液池。
实施例3
如图1所示,本实施例的石墨烯的制备方法按如下步骤进行:
(1)原矿处理:
将产自广东韶关的石墨含量为55%的石墨矿石水洗、晾干后,利用球磨机磨碎为200~300目的矿粉,再浮选矿粉至含碳量为80~90%的精矿粉,然后将精矿粉送入温度为2950℃的高温炉内气化除杂,再利用雷蒙机对高温除杂后的物料进行研磨,得到含碳量大于99%、2000目的石墨粉。
(2)液相剥离:
将步骤(1)所得石墨粉投入装有ph值为7.5的碳酸氢钠水溶液的碱液池中浸泡3h,并控制混合液中投加的石墨粉的质量百分比不超过0.5%,再将碱液池内的混合液送入搅拌桶中搅拌,然后将搅拌桶内的混合液通过射流管射流返回到碱液池,对混合液循环搅拌和射流操作共1.5h。
(3)后处理:
将步骤(2)处理所得的混合液送入沉淀池中沉淀2h,然后用2000目的滤网过滤,将所得滤渣返回到步骤(2)的碱液池,将所得滤液送入浮选机中进行泡沫浮选,并选用酚黑药作为浮选药剂,浮选时往每吨滤液中投加2g氧烷醇黑药。浮选后,捞取液面的泡沫,用铜片制成的输送带将泡沫送入干燥室内以70℃的温度进行干燥,得到石墨烯,然后对石墨烯包装、入库,浮选后剩余滤液则返回到步骤(2)的碱液池。
实施例4
如图1所示,本实施例的石墨烯的制备方法按如下步骤进行:
(1)原矿处理:
将产自广东韶关的石墨含量为60%的石墨矿石水洗、晾干后,利用球磨机磨碎为200~300目的矿粉,再浮选矿粉至含碳量为80~90%的精矿粉,然后将精矿粉送入温度为3000℃的高温炉内气化除杂,再利用雷蒙机对高温除杂后的物料进行研磨,得到含碳量大于99%、2400目的石墨粉。
(2)液相剥离:
将步骤(1)所得石墨粉投入装有ph值为7.8的碳酸氢钠水溶液的碱液池中浸泡2h,并控制混合液中投加的石墨粉的质量百分比不超过0.5%,再将碱液池内的混合液送入搅拌桶中搅拌,然后将搅拌桶内的混合液通过射流管射流返回到碱液池,对混合液循环搅拌和射流操作共2h。
(3)后处理:
将步骤(2)处理所得的混合液送入沉淀池中沉淀2h,然后用2400目的滤网过滤,将所得滤渣返回到步骤(2)的碱液池,将所得滤液送入浮选机中进行泡沫浮选,并选用酚黑药作为浮选药剂,浮选时往每吨滤液中投加2g酚黑药。浮选后,捞取液面的泡沫,用铜片制成的输送带将泡沫送入干燥室内以75℃的温度进行干燥,得到石墨烯,然后对石墨烯包装、入库,浮选后剩余滤液则返回到步骤(2)的碱液池。
按本发明的制备方法实施,每吨混合液可制备得到300~500g石墨烯产品。请参阅图2,通过显微设备能观察到本发明所得石墨烯样品中的六角型蜂巢晶格,所得石墨烯样品为单层平面薄膜结构。
以上所述实施例仅表达了本发明的几种实施方式,其描述较为具体和详细,但并不能因此而理解为对发明专利范围的限制。应当指出的是,对于本领域的普通技术人员来说,在不脱离本发明构思的前提下,还可以做出若干变形和改进,这些都属于本发明的保护范围。
技术研发人员:邓功甫
技术所有人:邓功甫
备 注:该技术已申请专利,仅供学习研究,如用于商业用途,请联系技术所有人。
声 明 :此信息收集于网络,如果你是此专利的发明人不想本网站收录此信息请联系我们,我们会在第一时间删除